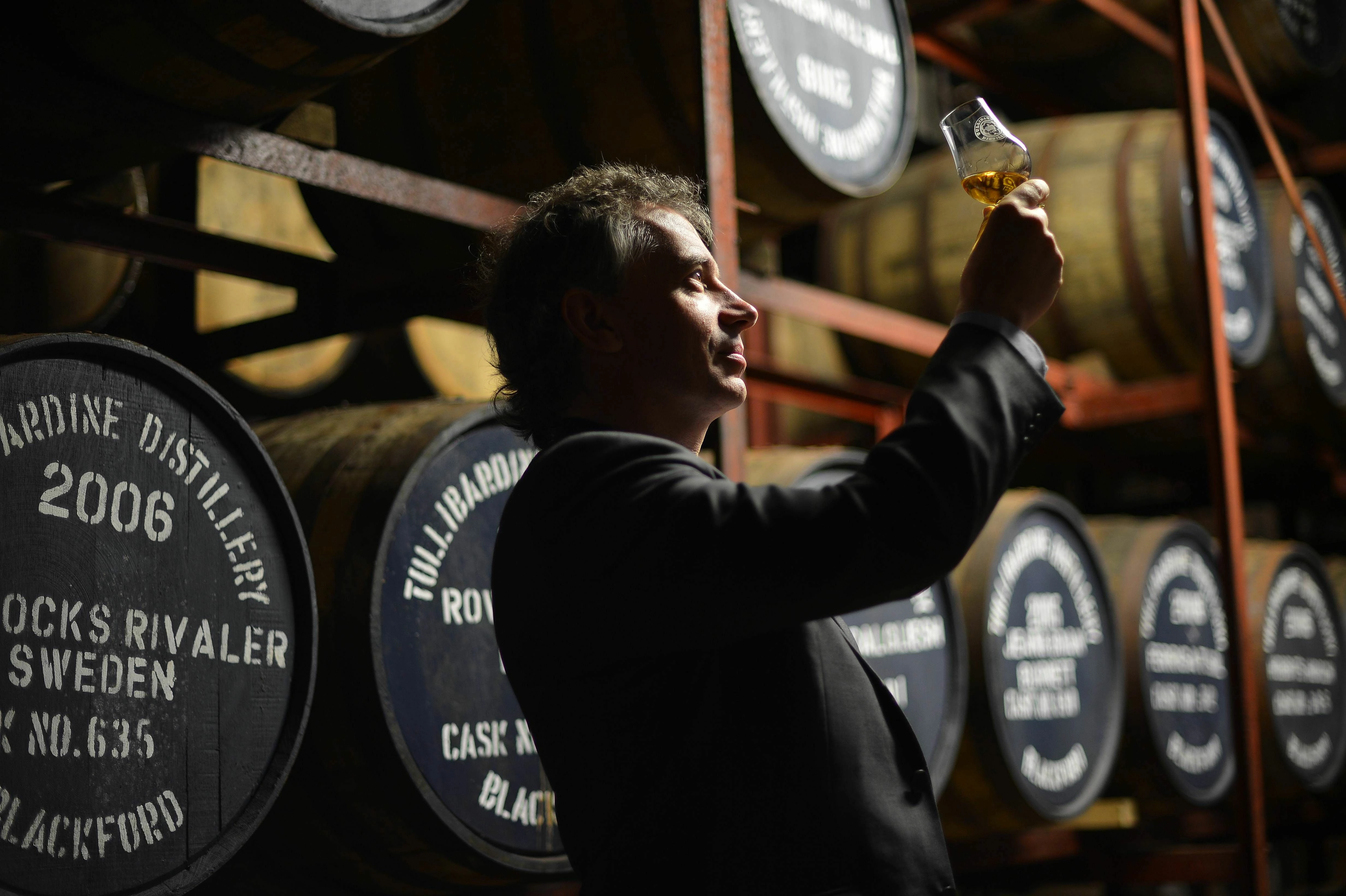
Partner Article
Whisky Distillery Converts Waste To Biofuel At CPI
A Scottish whisky is set to become the first in the world to have its waste by-products converted into advanced biofuel, capable of powering vehicles fuelled by petrol or diesel.
Tullibardine, an independent malt whisky producer in Blackford, Perthshire has signed a memorandum of understanding with Celtic Renewables Ltd which has developed the technology to produce biobutanol from the by-products of whisky production.
The distillery is currently supplying raw materials to help refine the conversion process at the Centre for Process Innovation (CPI) at Redcar, in Teesside.
Celtic Renewables, a spin-out company from the Biofuel Research Centre (BfRC) at Edinburgh Napier University, aims to build a processing plant in Scotland that will help grow a projected £60million-a-year industry.
Tullibardine has the capacity to provide 6,500 tonnes of draff and 2 million of litres of pot ale, the by-products of whisky which are currently spread on agricultural fields, turned into animal feed or safely discharged into the sea under license, all at significant cost.
The project has the support of ministers who believe it can contribute to the Scottish Government’s target of reducing carbon emissions by 42% by 2020 as well as contributing to the EU mandated biofuel target of 10% by 2020.
Douglas Ross, the managing director of Tullibardine, which spends £250,000 disposing of its by-products every year, said: “We are delighted to be partnering Celtic Renewables in this innovative venture, the obvious benefits of which are environmental. It takes a cost to us and turns it into something that has social as well as commercial value.”
The pilot demonstration project is being funded with the help of a £155,000 grant from Zero Waste Scotland. Iain Gulland, Director of Zero Waste Scotland, said “To become a zero waste society we need to find new, innovative ways of turning wastes and by-products into high-quality products.
“As well as having clear environmental benefits, this project has the potential to lead the way in realising cost savings across Scotland’s whisky industry, unlocking hidden value and helping to boost the economy.”
Professor Martin Tangney, director of the BfRC who is the company’s founder and chief scientific officer, said: “Our partnership with Tullibardine is an important step in the development of a business which combines two iconic Scottish industries – whisky and renewables.
“This project demonstrates that innovative use of existing technologies can utilise resources on our doorstep to benefit both the environment and the economy.”
While the original “proof-of-concept” research, conducted at Edinburgh Napier, was at a small lab-scale of three litres of pot ale, this industrial scale second phase testing at the CPI will systematically scale up to 10,000 litres.
“By piloting the fermentation at commercial scale we will demonstrate the viability of the process as a new and important industry of potential scale for Scotland”, says Mark Simmers, CEO of Celtic Renewables.
Because distilleries currently produce around three times more pot ale than draff, the company is also considering other sustainable sources of sugar-rich raw materials, such as the by-products from breweries or paper waste, to help it convert the excess into biofuel.
“If we were to use all the by-products from Scottish distilleries, it would still leave us with almost 1.5billion litres of pot ale,” observed Simmers.
“We could make at least the same volume of fuels again by using alternative waste or residue material such as paper and brewery waste.”
Ends
Notes to Editors
For more information contact Kathryn Clapham at Velvet Communications on 01642 584790 or email kathryn@velvetcommunications.co.uk.
About CPI:
The Centre for Process Innovation is a UK-based technology innovation centre and part of the High Value Manufacturing Catapult. We use applied knowledge in science and engineering combined with state of the art facilities to enable our clients to develop, prove, prototype and scale up the next generation of products and processes.
Our open innovation model enables clients to develop products and prove processes with minimal risk. We provide assets and expertise so our customers can demonstrate the process and show it is feasible before investing substantial amounts of money in capital equipment and training. New products and processes can be proven; on paper, in the lab and in the plant before being manufactured at an industrial scale.
By utilising our proven assets and expertise companies can take their products and processes to market faster. There is no down time in production as all of the process development is completed offsite and our technology transfer teams can help you to transfer the product or process into full scale production at speed.
The Biofuel Research Centre was established by Professor Martin Tangney at Edinburgh Napier University in December 2007.It was the first such centre of its kind, set up for the purpose of developing sustainable biofuels.At present some 97% of Tullibardine’s whisky by-products are disposed of after production. They include draff – the sugar rich kernels of barley which are soaked in water to facilitate the fermentation process – and pot ale, the yeasty liquid that is heated during distillation.A bacterial fermentation process known as Acetone-butanol-ethanol (ABE) produces acetone, n-Butanol, and ethanol from starch.The production of butanol by biological means was first performed by Louis Pasteur in 1861.Industrial exploitation of ABE fermentation started in 1916 with Chaim Weizmann’s isolation of Clostridium acetobutylicum.Scotland’s distilleries currently produce around 600,000 tonnes of draff and 2billion litres of pot ale.The CPI helps companies to prove and scale up processes to manufacture new products and create more sustainable, efficient and economic industries of the future.
This was posted in Bdaily's Members' News section by Kathryn Clapham .