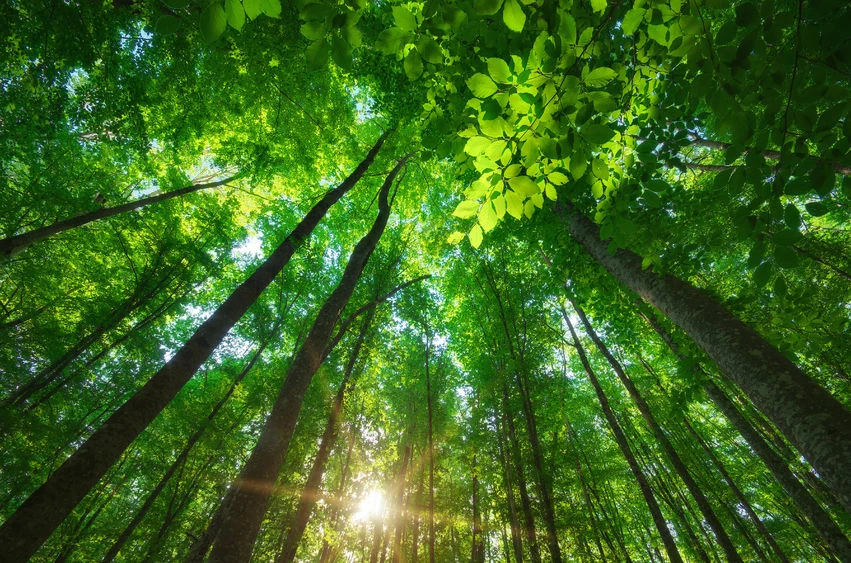
Partner Article
The Vita Groups aims for 50% of products to have sustainable alternatives by 2030
The Vita Group, Europe’s leading flexible foam solutions provider, has launched a bold new sustainability strategy laying down the group’s aspirations and objectives across the full range of its product portfolio.
The ambitions, which include aiming for half of its product range to have a sustainably-sourced option by 2030, are intended to further accelerate the company’s commitment to both sustainability and innovation.
Its ‘Enhancing Everyday Life’ strategy will enable The Vita Group - which employs 2,700 people across Europe and is headquartered in Manchester - to further develop its Environmental, Social and Governance (ESG) strategy.
The roadmap for the next three decades includes; aiming for the use of 100% renewable electricity across all Vita plants by 2030; a desire to be Scope 1 and Scope 2 carbon neutral across all wholly-owned manufacturing operations by 2050; as well as ensuring that no manufacturing waste is taken to landfill after 2040, an ambition which it has already achieved across two of its largest sites at Middleton and Accrington.
The Vita Group boasts a long history of innovation in sustainability and has been making industry-leading products from 100% recycled PU foam for over 50 years. It recycles and re-bonds over 30,000T of its own and its customer’s process trim each year into a range of products from carpet underlay, foam shock pad for artificial sports pitches, materials for green roof applications and many more upcycling solutions.
The company anticipates Enhancing Everyday Life will inspire businesses from within its supply chain and the wider foam industry to follow its lead and set similar goals to help drive the momentum for more sustainable manufacturing materials and processes.
To achieve these targets, The Vita Group will harness the potential of its four state-of-the-art innovation centres in Accrington, Lithuania, Corby and Middleton which cater to emerging customer needs through developments in chemistry, processing, material usage and new product research. Recently, The Vita Group’s Middleton Innovation Centre developed FRee foam, an environmentally-friendly alternative to standard foams that is fully compliant with UK flammability regulations.
Other recent investments include a new collaboration with Dow on its ground-breaking RENUVA™ Mattress Recycling Program. The partnership involves mattresses being processed through Dow’s in-house technology and converted back into a base raw material used to make brand new foam for a variety of applications, including mattresses. Production quantities of foam will be manufactured using RENUVA™ Polyols at Vita’s production site at ICOA in Crancey, north-central France.
The company is on track with its ambitious plans. As of March 2021, it has already put in place measures to ensure that all new projects in the innovation pipeline have sustainability built in. It is also continuing to lead the way by creating a range of sustainable polyols, including CO2 derived polyols and renewable polyols from sustainable sources (e.g., soya bean and castor oil). The Vita Group’s new sustainability strategy aims for all foaming facilities to be capable of producing foams using sustainable polyols by 2030.
Ian Robb, Group CEO at The Vita Group, said: “Sustainability is integral to our culture, purpose, and values. We have a long history of innovation in sustainability, investing in circular economy products and using lower carbon and more sustainable alternative raw materials. Our new Enhancing Everyday Life strategy lays out our ambitious plan to continue leading the ESG agenda within our industry.
“Thanks to our state-of-the-art innovation centres we will accelerate our product and service capabilities in line with eco-friendly options. While we are seeing a greater demand from customers for more sustainable products, we also see it as our responsibility to innovate in order to develop a circular economy that will help reduce carbon outputs and increase End Of Life (EOL) recycling.
“By announcing and implementing these new pledges, we look to inspire others across the manufacturing sector to set similar targets so we can all work collaboratively to achieve higher and greener standards across the industry, in order to help protect the world around us for future generations.”
This was posted in Bdaily's Members' News section by Sarah Jones .