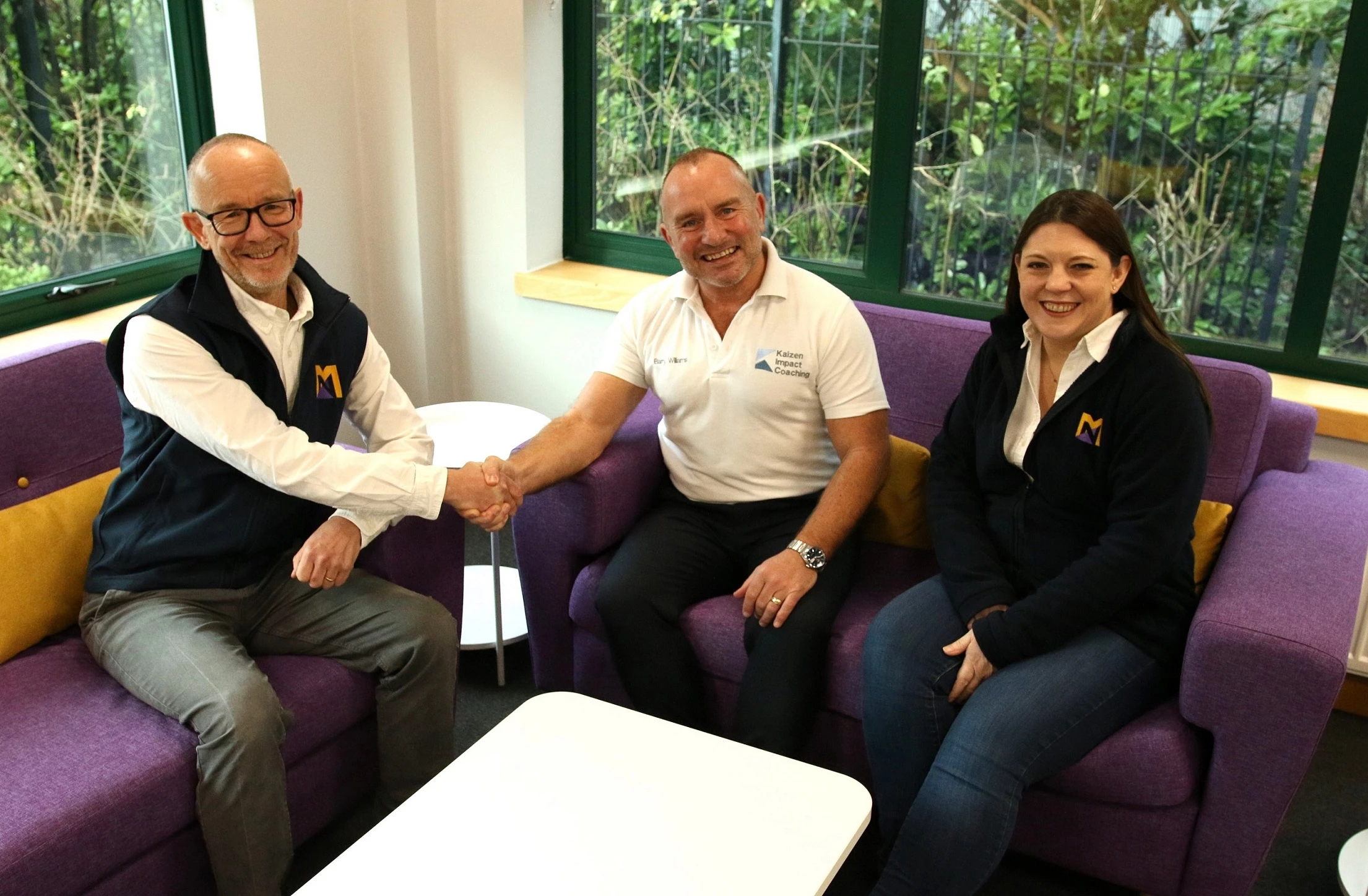
Doncaster firm forges new partnership to increase manufacturing productivity
A Doncaster based business has launched a new support programme to give manufacturing firms the chance to make efficiency gains and significantly reduce their operating costs.
Kaizen Impact Coaching has joined forces with the Manufacturers Network to deliver the Productivity and Capability Energiser programme (PaCE).
The new partnership provides manufacturing leaders and their management teams with 15 days of intensive targeted support from two specialist coaches over a five-month period. It is designed to help them improve manufacturing productivity by optimising processes, maximising value, standardising work and strengthening leadership.
Participants will build capability and make improvements using proven Kaizen techniques including value stream mapping, process observation and practical problem solving. They will also attain the Lean Competency System (LCS) accreditation from Cardiff University.
Barry Williams from Kaizen Impact Coaching, who has worked for global manufacturers such as Jaguar Land Rover, Rolls Royce and Airbus explains: “Over the five months, we deliver each step in individual blocks, with the pace set to deliver the greatest potential for learning.
“Our purpose is to deliver high impact improvement, in a scalable, high value, easy to follow approach that can be used forever. We’ll be working with the manufacturers to build their capability to see things differently, use facts and data, and understand where and how they can make improvements.
“We’ll be providing them with everything they need to make sustainable improvement in targeted areas. They will develop wider knowledge, skills, tools and confidence to deliver improvement across their business. The benefits and potential of the approach are huge, and so too the value.”
Chris Merriman from the Manufacturers Network adds: “Our new programme affords manufacturing leaders and managers time they never usually get to take a step back from their business and analyse where productivity, processes and workflow can be improved.
“More importantly, they get to work with a highly effective specialist Kaizen coaching team on identifying opportunities to increase productivity and reduce costs. Participants attend for three days each month to receive intensive coaching which includes improving workflow and identifying activities to achieve the highest return on investment and longer-term financial benefits.
“They then have the chance to start applying identified improvements and benchmarking progress at the end of the programme.”
By working with other manufacturing firms during the programme, the aim is that participants will also benefit by growing their networks, sharing best practice and encouraging more collaborative ways of working.
By Mark Adair – Correspondent, Bdaily
- Add me on LinkedIn and Twitter to keep up to date
- And follow Bdaily on Facebook, Twitter and LinkedIn
- Submit press releases to editor@bdaily.co.uk for consideration.
Looking to promote your product/service to SME businesses in your region? Find out how Bdaily can help →
Enjoy the read? Get Bdaily delivered.
Sign up to receive our popular Yorkshire & The Humber morning email for free.